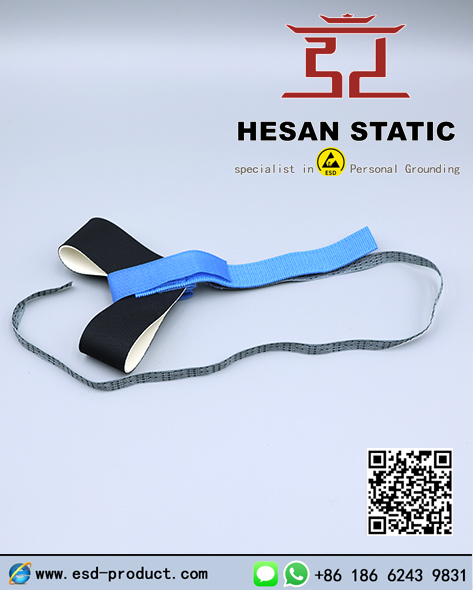
Selection of ESD protection devices and what are the design requirements?
Electrostatic discharge (ESD) is a natural phenomenon that generates electromagnetic fields that can interfere with the proper operation of electronic equipment. In the design and production process of electronic products, the design of ESD protection circuit is very important. This article will introduce the selection and design requirements of ESD protection devices in detail, including circuit structure, component selection, layout and wiring, testing and optimization, etc.
During the manufacturing process, the prevention of electrostatic discharge is based on the Electrostatic Discharge Protected Area (EPA). An EPA can be a small workstation or a larger production area. The main rationale of the EPA is that there are no highly charged materials in the vicinity of ESD sensitive electronics, all conductive and dissipative materials are grounded, personnel are grounded, and the buildup of charge on ESD sensitive electronics is prevented. International standards are used to define typical EPAs, such as can be found from the International Electrotechnical Commission (IEC) or the American National Standards Institute (ANSI).
Electrostatic discharge precautions in the EPA include the use of appropriate ESD-safe packaging materials, the use of conductive filaments on clothing worn by assembly workers, conductive wrist and foot straps to prevent high voltages from building up on workers' bodies, anti-static mats, or conductive floors. Materials carry unwanted charges away from the work area and control humidity. Humid conditions prevent electrostatic charges from developing because a thin layer of moisture that accumulates on most surfaces can dissipate the charge.
An ESD event indicates a buildup of electrostatic charge, which occurs when two dissimilar conductive materials or conductors rub together. One of the materials is positively charged; the other is negatively charged. If a material now carries a substantial static charge, when this charged object comes into contact with another conductive material, the static is transferred and an ESD event occurs.
Electronics manufacturers employ a variety of ESD protection measures to prevent problems during the manufacturing process, including fabrication, testing, shipping, and handling.
1. Selection of ESD protection devices
1. Selection according to circuit power
When selecting an ESD protection device, the power consumption of the circuit needs to be considered. For high power applications, it may be necessary to select a device with a higher withstand voltage to ensure that damage does not occur during an ESD event.
2. Selection according to the value of the inductor and capacitor
The inductance and capacitance values of an ESD protection device also affect its performance. In high-speed signal transmission, it is necessary to select devices with lower inductance values and higher capacitance values to provide better signal integrity.
3. Selection according to application scenarios
Different application scenarios have different requirements for ESD protection devices. For example, in industrial control systems, it may be necessary to select devices with higher sensitivity to ensure normal operation in harsh electrostatic environments.
2. Design requirements of ESD protection devices
1. Voltage requirements
ESD protection devices must be able to withstand the voltage generated by an electrostatic discharge event to avoid damage to internal circuitry. Therefore, when designing an ESD protection device, it is necessary to ensure that its withstand voltage is sufficiently high.
2. Anti-jamming capability requirements
ESD protection devices must have good noise immunity to avoid misoperation of internal circuits during electrostatic discharge events. Therefore, when designing an ESD protection device, it is necessary to ensure that its anti-interference performance meets relevant standards.
3. Temperature stability requirements
ESD protection devices must have good temperature stability to ensure proper operation over a wide temperature range. Therefore, when designing an ESD protection device, it is necessary to analyze its temperature characteristics in detail and make necessary optimizations.
4. Anti-corrosion requirements
ESD protection devices must have good corrosion resistance to avoid corrosion during long-term use. Therefore, when designing ESD protection devices, appropriate anti-corrosion measures, such as metal passivation, coating, etc., need to be adopted.
3. Practical application case analysis
Take a mobile phone circuit board as an example, which contains multiple ESD protection devices. In the design process, a variety of implementation methods have been adopted, including bus control, power amplifier and input and output modules. In practical applications, an appropriate implementation method should be selected according to specific requirements, and tested and optimized to improve ESD protection capabilities.
4. Conclusion
This paper introduces the selection and design requirements of ESD protection devices in detail, including circuit structure, component selection, layout and wiring, testing and optimization, etc. In practical applications, appropriate ESD protection devices should be selected according to specific needs, and tested and optimized to improve the safety and reliability of the circuit.